Renovierer60
2019-06-14 11:32:07
- #1
Hello everyone!
I have a not entirely trivial, but certainly often occurring renovation problem or undertaking.
Old: built in the 50s, roller shutter box with inspection cover (thin wood) on the inside, basically complete cold and air infiltration to the inside – perfect for mold, a disaster for the oil heating system.
New: external roller shutter boxes (Raffstorekästen) will be installed on the outside wall, the new windows have been set outward and are now located under the approximately 8 cm thick concrete lintel panel. The roller shutter boxes are in front of this panel and then disappear into the ETICS (stone wool) layer.
Problem or weak point 1: between cold outside air and interior there are only 8 cm of concrete.
Problem or weak point 2: dew point issue.
Solution 1) between the upper window frame and the concrete lintel panel 2 cm foam, because better than frame on concrete and better insulation value = implemented.
Solution 2) insulation to be installed between roller shutter box and concrete lintel outside > not possible, as otherwise it would become too thick and more than 14 cm ETICS would be needed.
Solution 3) the old box on the inside is completely insulated and sealed airtight (possibly electrical cable routed to the outside, inspection from outside, but if insulation requires it, the electrical cable can also be routed elsewhere).
The energy consultant gave the general feasibility a green light, the fRsi value is not so great but feasible.
Regarding solution 3, so that everything fits thermally, with respect to mold, and stability, I now have questions:
a) which trade is my guy here?
- Drywaller, but not his specialty
- Plasterer/insulator
- special insulation company that also does the necessary (?) drywall finishing?!
b) what is the best insulation material for this?
- stone wool
- Styrodur
- brick (I view critically because of the fastening possibility especially with larger/longer boxes like in the living room)
c) the lower closure, where the inspection cover was before, should it run against the wooden frame? Closure with silicone joint? I think yes, the alternative would be a bit higher against the 2cm foam, but that would then be a new weak point.
d) alternatively asked: what would you recommend? (please do not suggest alternatives like demolition etc. – the windows are set :-)
Many thanks for your help and advice!
Regarding the pictures:
- Dew point calculation
- Example picture, turquoise: future insulation, blue: 2cm foam
- most windows are open at the bottom with an existing mortar plaster panel on the room side
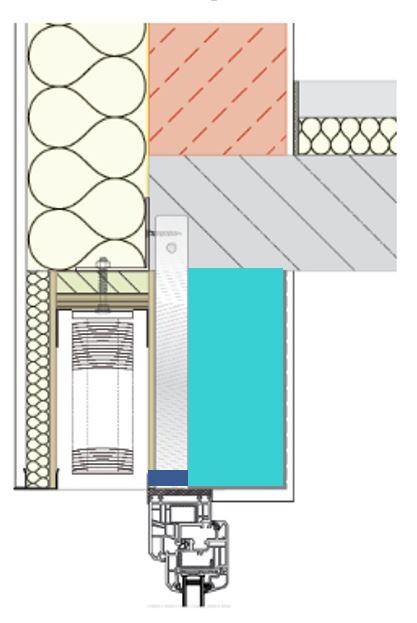
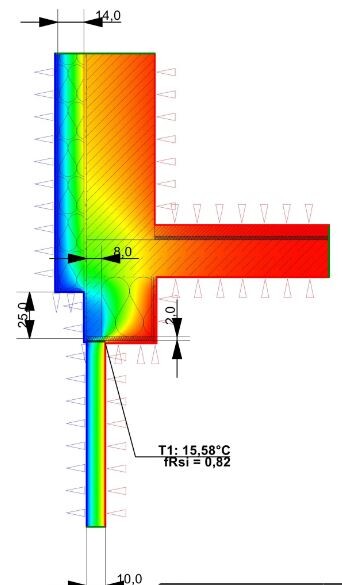
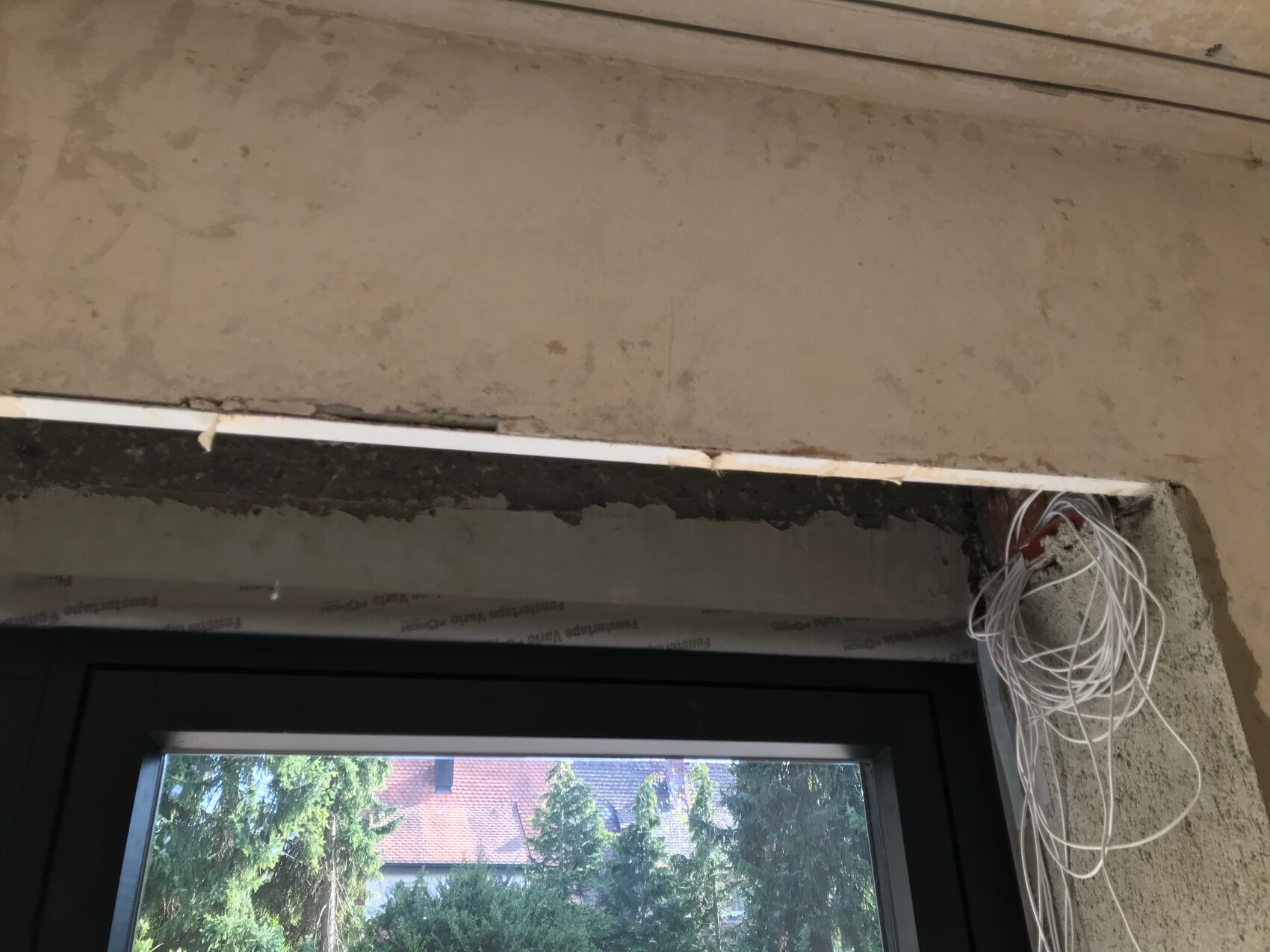
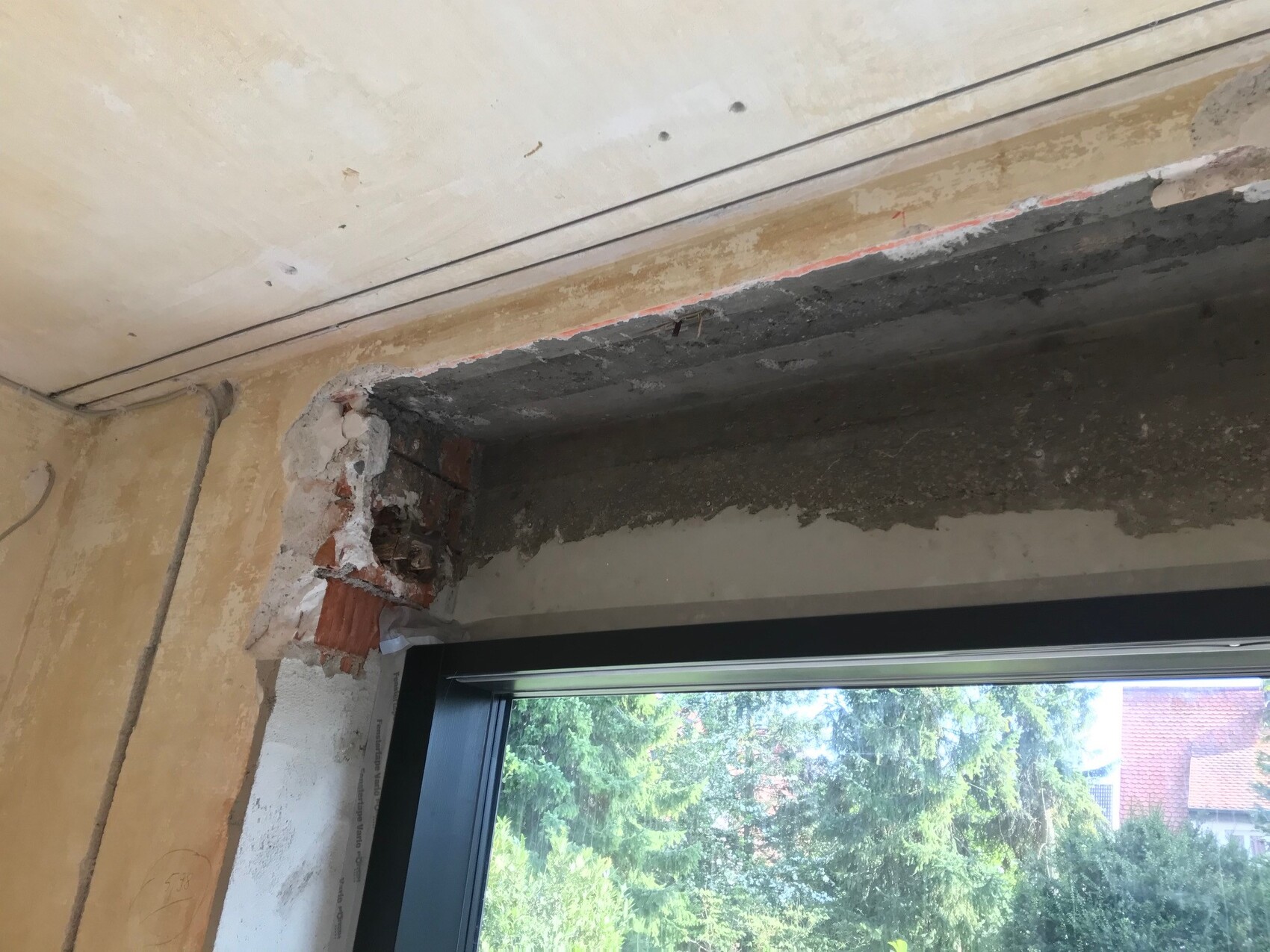
I have a not entirely trivial, but certainly often occurring renovation problem or undertaking.
Old: built in the 50s, roller shutter box with inspection cover (thin wood) on the inside, basically complete cold and air infiltration to the inside – perfect for mold, a disaster for the oil heating system.
New: external roller shutter boxes (Raffstorekästen) will be installed on the outside wall, the new windows have been set outward and are now located under the approximately 8 cm thick concrete lintel panel. The roller shutter boxes are in front of this panel and then disappear into the ETICS (stone wool) layer.
Problem or weak point 1: between cold outside air and interior there are only 8 cm of concrete.
Problem or weak point 2: dew point issue.
Solution 1) between the upper window frame and the concrete lintel panel 2 cm foam, because better than frame on concrete and better insulation value = implemented.
Solution 2) insulation to be installed between roller shutter box and concrete lintel outside > not possible, as otherwise it would become too thick and more than 14 cm ETICS would be needed.
Solution 3) the old box on the inside is completely insulated and sealed airtight (possibly electrical cable routed to the outside, inspection from outside, but if insulation requires it, the electrical cable can also be routed elsewhere).
The energy consultant gave the general feasibility a green light, the fRsi value is not so great but feasible.
Regarding solution 3, so that everything fits thermally, with respect to mold, and stability, I now have questions:
a) which trade is my guy here?
- Drywaller, but not his specialty
- Plasterer/insulator
- special insulation company that also does the necessary (?) drywall finishing?!
b) what is the best insulation material for this?
- stone wool
- Styrodur
- brick (I view critically because of the fastening possibility especially with larger/longer boxes like in the living room)
c) the lower closure, where the inspection cover was before, should it run against the wooden frame? Closure with silicone joint? I think yes, the alternative would be a bit higher against the 2cm foam, but that would then be a new weak point.
d) alternatively asked: what would you recommend? (please do not suggest alternatives like demolition etc. – the windows are set :-)
Many thanks for your help and advice!
Regarding the pictures:
- Dew point calculation
- Example picture, turquoise: future insulation, blue: 2cm foam
- most windows are open at the bottom with an existing mortar plaster panel on the room side